Snake-like, miniature robots redefine limits of engineering
Maintenance and repair of high-tech equipment revolutionized by research innovations
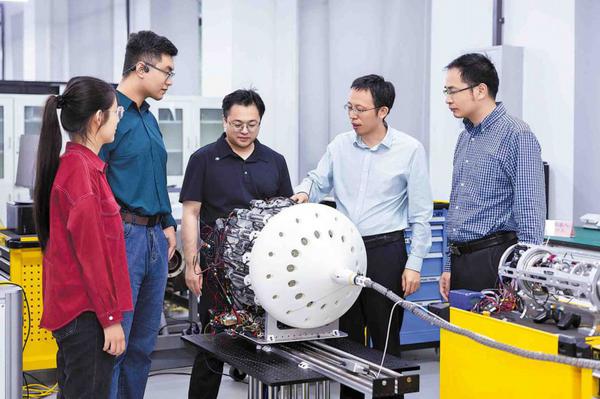
Chen Xuefeng (second from right) leads a group discussion with team members last month at Xi'an Jiaotong University in Xi'an, Shaanxi province. (CHINA DAILY)
With the completion and opening of projects such as the China-Laos Railway and the Jakarta-Bandung High-Speed Railway in Indonesia, along with the breakthroughs in domestic large aircraft and the aeroengine systems, the export volume of Chinese high-speed trains and airplane parts has been gradually increasing in recent years.
As a result, the maintenance of high-end equipment through innovation has become a major focus for Chinese researchers.
A team led by Chen Xuefeng, a professor at the iHarbour Academy of Frontier Equipment based at Xi'an Jiaotong University in Shaanxi province, has developed a biomimetic, snake-shaped robot that is forecast to revolutionize maintenance and repair work. The robot snake is capable of performing automated blade damage inspections without dismantling precision equipment like aeroengines, and can do other high-end equipment maintenance.
"In the past, inspecting an aeroengine required multiple technicians to work continuously in confined spaces for hours or to completely dismantle the engine, which was time-consuming and exhausting," said Chen.
"But in the future, our biomimetic robots will be able to perform minimally invasive maintenance without disassembling the engine. We can describe it as 'industrial minimally invasive surgery'," he said.
Last summer, Chen's team developed the insect-sized BATE (Boundary Actuation Tunable Energy-barrier) Jumper, a miniature robot with a strong jumping ability. This robot, only 15 millimeters in length, can jump 12.7 times its length vertically, and cover 20 times its length horizontally. Due to its compact and flexible design, the BATE Jumper has unique advantages in confined spaces and complex environments, making it extremely promising in fields such as exploration, search and rescue.
Complex applications
However, the team did not stop there. They targeted more complex application scenarios in the field of flexible continuum snake robots — particularly the inspection of aeroengines without the need to remove and dismantle them.
"The inside of an engine is like a metallic labyrinth," said Yang Laihao, an associate research fellow in the field of aeroengines at Xi'an Jiaotong University.
"In such complex and confined spaces, traditional rigid robotic arms struggle, whereas flexible continuum robots have great potential due to their superior dexterity and environmental adaptability," he said.
"However, current joint configuration designs face issues such as instability under compression, poor torsional performance, and insufficient load capacity. Additionally, under the influence of factors like gravity and friction, the end positioning error of these flexible continuum robots can increase exponentially with length, which remains a major obstacle to their practical application," he added.
To address these challenges, the team proposed several new joint designs from concepts such as contact-aided and active-passive hybrid configurations. They helped achieve a more than hundredfold improvement in bending stiffness, a twentyfold increase in torsional stiffness, and solved instability issues.
Yang said they have now achieved efficient and high-precision modeling of continuum robots, with efficiency reaching the millisecond level and repeat positioning accuracy now at the millimeter level.
The team has also developed multiple types of continuum robot systems for the maintenance of high-end equipment. They include fully active continuum robots with a length-to-diameter ratio exceeding 80, and active-passive continuum robots that can extend to several meters. These have been validated in various aviation equipment applications.
"I have seen aeroengine inspection technicians climb into long-narrow inlets to manually inspect blade cracks with flashlights. This often results in lumbar spine injuries, requiring job rotation every six months," Chen said, citing field surveys.